Photovoltaikmodule - wie sind sie aufgebaut?
[Dünnschicht und Dickschicht]
Photovoltaikmodule, dünn oder dick: Schicht für Schicht
Photovoltaikmodule montiert:
Die Solarstromernte kann beginnen
Photovoltaik-Module sind die Stromfabriken im komplexen Gefüge der Photovoltaikanlage. Sie fangen die Energie des Sonnenlichts ein und wandeln sie in elektrische Energie um.
In den letzten Jahrzehnten haben wir uns an ihren Anblick gewöhnt - wegen ihres effizienten Designs wirken sie einfach und fast schon alltäglich. Aber als echte Kunstwerke aus Physik und Ingenieurswissenschaften sind sie doch um Einiges raffinierter, als sie auf den ersten Blick aussehen.
Lesen Sie hier alles Wissenswerte über den Aufbau von Photovoltaik-Modulen!
Inhaltsverzeichnis:
Das Gestaltungsprinzip von Photovoltaikmodulen
Das Gestaltungsprinzip, dem sich im Aufbau von Photovoltaikmodulen jedes einzelne Detail unterordnet - wie beim Aufbau der Photovoltaikanlage insgesamt -, ist ihre Funktion:
Die kostengünstige und verlässliche Erzeugung von Solarstrom unter wechselnden Witterungsbedingungen auf Jahrzehnte hinaus.
Im Kleinen ist dies die Aufgabe der Solarzellen, der Arbeiter in der PV-Anlage – einige Zehntel bis wenige Tausendstel Millimeter feine Fotodioden, die im Kern der Module ihren Dienst verrichten. Im größeren Maßstab wird deren Leistung im Photovoltaik-Modul gebündelt, mit der Leistung anderer PV-Module verschaltet und weitergegeben an den Wechselrichter der Anlage und zur Anschlussstelle.
Einfangen lässt sich die Sonne aber nur draußen - unter freiem Himmel. Dort sind die sensiblen Bauteile unweigerlich Wind und Wetter, Hitze und Kälte, Staub und Schmutz ausgesetzt - 24 Stunden am Tag und 365 Tage im Jahr.
Um einen langandauernden, reibungslosen und möglichst einträglichen Betrieb der Solarstromanlage garantieren zu können, müssen PV-Module deshalb drei Herausforderungen meistern:
- Die vor Ort verfügbare Sonnenenergie muss so effizient wie möglich in Solarstrom umgewandelt werden.
- Die Module müssen zuverlässig wechselnden Witterungsbedingungen standhalten – und dies während der ganzen Laufzeit der Anlage, in der Regel 25 bis 40 Jahre lang.
- Die Solarpaneele sollten in einem günstigen Preis-Leistungsgefüge einfach und rasch, stabil und dachschonend montiert werden können.
Diese Herausforderungen sind es, die den Aufbau der Module im Grundsatz diktieren. Wie der aber im Detail, nämlich Schicht für Schicht aussieht, das hängt vom verwendeten Solarzellentyp ab. Module aus kristallinen Solarzellen sind gänzlich anders aufgebaut als Dünnschichtmodule. Im Folgenden zeigen wir Ihnen, wie.
-
Solarmodule für Ihr Dach?
In unserem Angebots- und Preisvergleich rechnen Solarteure vor Ort kostenlos und unverbindliche Kosten und Einnahmen individuell für Sie durch:
Photovoltaikmodule, dünn oder dick: Schicht für Schicht
Photovoltaikmodule montiert:
Die Solarstromernte kann beginnen
Photovoltaik-Module sind die Stromfabriken im komplexen Gefüge der Photovoltaikanlage. Sie fangen die Energie des Sonnenlichts ein und wandeln sie in elektrische Energie um.
In den letzten Jahrzehnten haben wir uns an ihren Anblick gewöhnt - wegen ihres effizienten Designs wirken sie einfach und fast schon alltäglich. Aber als echte Kunstwerke aus Physik und Ingenieurswissenschaften sind sie doch um Einiges raffinierter, als sie auf den ersten Blick aussehen.
Lesen Sie hier alles Wissenswerte über den Aufbau von Photovoltaik-Modulen!
Inhaltsverzeichnis:
Das Gestaltungsprinzip von Photovoltaikmodulen
Das Gestaltungsprinzip, dem sich im Aufbau von Photovoltaikmodulen jedes einzelne Detail unterordnet - wie beim Aufbau der Photovoltaikanlage insgesamt -, ist ihre Funktion:
Die kostengünstige und verlässliche Erzeugung von Solarstrom unter wechselnden Witterungsbedingungen auf Jahrzehnte hinaus.
Im Kleinen ist dies die Aufgabe der Solarzellen, der Arbeiter in der PV-Anlage – einige Zehntel bis wenige Tausendstel Millimeter feine Fotodioden, die im Kern der Module ihren Dienst verrichten. Im größeren Maßstab wird deren Leistung im Photovoltaik-Modul gebündelt, mit der Leistung anderer PV-Module verschaltet und weitergegeben an den Wechselrichter der Anlage und zur Anschlussstelle.
Einfangen lässt sich die Sonne aber nur draußen - unter freiem Himmel. Dort sind die sensiblen Bauteile unweigerlich Wind und Wetter, Hitze und Kälte, Staub und Schmutz ausgesetzt - 24 Stunden am Tag und 365 Tage im Jahr.
Um einen langandauernden, reibungslosen und möglichst einträglichen Betrieb der Solarstromanlage garantieren zu können, müssen PV-Module deshalb drei Herausforderungen meistern:
- Die vor Ort verfügbare Sonnenenergie muss so effizient wie möglich in Solarstrom umgewandelt werden.
- Die Module müssen zuverlässig wechselnden Witterungsbedingungen standhalten – und dies während der ganzen Laufzeit der Anlage, in der Regel 25 bis 40 Jahre lang.
- Die Solarpaneele sollten in einem günstigen Preis-Leistungsgefüge einfach und rasch, stabil und dachschonend montiert werden können.
Diese Herausforderungen sind es, die den Aufbau der Module im Grundsatz diktieren. Wie der aber im Detail, nämlich Schicht für Schicht aussieht, das hängt vom verwendeten Solarzellentyp ab. Module aus kristallinen Solarzellen sind gänzlich anders aufgebaut als Dünnschichtmodule. Im Folgenden zeigen wir Ihnen, wie.
-
Solarmodule für Ihr Dach?
In unserem Angebots- und Preisvergleich rechnen Solarteure vor Ort kostenlos und unverbindliche Kosten und Einnahmen individuell für Sie durch:
Photovoltaikmodule, dünn oder dick: Schicht für Schicht
Photovoltaikmodule montiert:
Die Solarstromernte kann beginnen
Photovoltaik-Module sind die Stromfabriken im komplexen Gefüge der Photovoltaikanlage. Sie fangen die Energie des Sonnenlichts ein und wandeln sie in elektrische Energie um.
In den letzten Jahrzehnten haben wir uns an ihren Anblick gewöhnt - wegen ihres effizienten Designs wirken sie einfach und fast schon alltäglich. Aber als echte Kunstwerke aus Physik und Ingenieurswissenschaften sind sie doch um Einiges raffinierter, als sie auf den ersten Blick aussehen.
Lesen Sie hier alles Wissenswerte über den Aufbau von Photovoltaik-Modulen!
Inhaltsverzeichnis:
Das Gestaltungsprinzip von Photovoltaikmodulen
Das Gestaltungsprinzip, dem sich im Aufbau von Photovoltaikmodulen jedes einzelne Detail unterordnet - wie beim Aufbau der Photovoltaikanlage insgesamt -, ist ihre Funktion:
Die kostengünstige und verlässliche Erzeugung von Solarstrom unter wechselnden Witterungsbedingungen auf Jahrzehnte hinaus.
Im Kleinen ist dies die Aufgabe der Solarzellen, der Arbeiter in der PV-Anlage – einige Zehntel bis wenige Tausendstel Millimeter feine Fotodioden, die im Kern der Module ihren Dienst verrichten. Im größeren Maßstab wird deren Leistung im Photovoltaik-Modul gebündelt, mit der Leistung anderer PV-Module verschaltet und weitergegeben an den Wechselrichter der Anlage und zur Anschlussstelle.
Einfangen lässt sich die Sonne aber nur draußen - unter freiem Himmel. Dort sind die sensiblen Bauteile unweigerlich Wind und Wetter, Hitze und Kälte, Staub und Schmutz ausgesetzt - 24 Stunden am Tag und 365 Tage im Jahr.
Um einen langandauernden, reibungslosen und möglichst einträglichen Betrieb der Solarstromanlage garantieren zu können, müssen PV-Module deshalb drei Herausforderungen meistern:
- Die vor Ort verfügbare Sonnenenergie muss so effizient wie möglich in Solarstrom umgewandelt werden.
- Die Module müssen zuverlässig wechselnden Witterungsbedingungen standhalten – und dies während der ganzen Laufzeit der Anlage, in der Regel 25 bis 40 Jahre lang.
- Die Solarpaneele sollten in einem günstigen Preis-Leistungsgefüge einfach und rasch, stabil und dachschonend montiert werden können.
Diese Herausforderungen sind es, die den Aufbau der Module im Grundsatz diktieren. Wie der aber im Detail, nämlich Schicht für Schicht aussieht, das hängt vom verwendeten Solarzellentyp ab. Module aus kristallinen Solarzellen sind gänzlich anders aufgebaut als Dünnschichtmodule. Im Folgenden zeigen wir Ihnen, wie.
-
Solarmodule für Ihr Dach?
In unserem Angebots- und Preisvergleich rechnen Solarteure vor Ort kostenlos und unverbindliche Kosten und Einnahmen individuell für Sie durch:
Der Aufbau von Dickschicht-Photovoltaikmodulen
- Kristalline Photovoltaik-Module: der Aufbau
- Dicksicht-PV-Module: die Herstellung
Wenn heute irgendwo auf der Welt - sei es auf einem Haus, einer Scheune oder einem Solarfeld - eine Photovoltaik-Anlage errichtet wird, dann kommen in 90 von 100 Bauvorhaben kristalline PV-Module zum Einsatz.
Ihr Marktanteil betrug im Jahr 2014 rund 91% (Quelle ISE Fraunhofer, PV-Report [engl.], S. 19).
Dieser Modultyp basiert - wie der Name schon sagt - auf kristallinen Solarzellen, die aus ca. 0,2 Millimeter dicken, rund 15 × 15 Zentimeter großen Silizium-Scheiben (Wafern) bestehen.
Die Bezeichnung „kristallin“ rührt übrigens von der Kristallstruktur der Silizium-Moleküle her. Die besonders hochwertigen Zellen aus monokristallinem Silizium bilden ein vollkommenes Kristallgitter, bei poly- bzw. multikristallinem Silizium ist es immer noch sehr gleichmäßig.
Landläufig werden die kristallinen Solarzellen oft auch Dickschichtzellen genannt: weil sie trotz ihrer geringen Stärke zehn bis hundert Mal dicker sind als Dünnschichtzellen.
Lesen Sie hier, wie Solarzellen aufgebaut sind und funktionieren.
Schicht für Schicht: der Aufbau kristalliner PV-Module im Detail
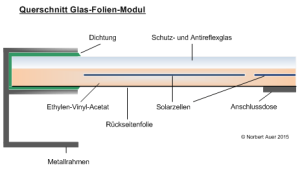
Damit ein Photovoltaikmodul elektrisch
und mechanisch einwandfrei funktioniert,
braucht es zahlreiche Schichten.
© Eigene Darstellung
Dickschicht-Module bestehen im Kern aus kristallinen Solarzellen.
Sie werden in einem von der Modulproduktion gesonderten Fertigungsprozess hergestellt. Das ist ein wesentlicher Unterschied zum Aufbau von Dünnschichtmodulen - ein Unterschied, der einerseits einen höheren technischen Aufwand und damit höhere Kosten verursacht.
Kristalline PV-Module sind nicht zuletzt deshalb pro Kilowatt Leistung ca. 200 bis 500 Euro teurer als Dünnschichtmodule.
Der höhere Herstellungsaufwand hat andererseits auch sein Gutes. Die Zellen lassen sich einzeln auf ihre Qualität prüfen, dabei können minderwertige Wafer aussortiert werden. Das ist einer der Gründe, weshalb kristalline Photovoltaikmodule bis heute einen um 5 bis 10% höheren Wirkungsgrad aufweisen als Dünnschicht-Paneele.
Wie Wafer von hoher Qualität hergestellt werden? Das
erfahren Sie in unserem Artikel über die Silizium-Scheiben.
Erst nach der Sortierung werden rund 30 bis 100 der ausgewählten kristallinen Zellen zum größeren funktionalen Ganzen des kristallinen PV-Moduls zusammengeschlossen.
Dieser gesonderte Fertigungsprozess dient unter anderem auch dazu, die hochsensiblen mikroelektronischen Bauteile, die das Licht in Strom umwandeln, in einen schützenden Kokon aus verschiedenen transparenten Schichten und Materialien einzuweben.
Und so sieht der typische Aufbau eines kristallinen PV-Moduls aus:
Bauteil des PV-Moduls | Funktion des Bauteils |
---|---|
Glasscheibe (Modulvorderseite) | - schützt vor Beschädigung - verbessert die Lichteinkopplung (höherer Wirkungsgrad) |
Solarzellen | - wandeln das Sonnenlicht in Strom um |
Folien aus Ethyl-Vinyl-Acetat (EVA); Ummantelung der Zellen | - die Folieneinbettung fixiert und schützt die Solarzellen |
Rückseitenfolie | - dient als Isolator und Schutz vor Feuchtigkeit |
Anschlussdose | - fasst die Kabel der Solarzellen zentral zusammen, damit die Module leichter miteinander verschaltet werden können - beherbergt die Bypass-Diode(n). Sie verringern Verluste durch teilweise Verschattung |
Dichtungen (zwischen Glasscheibe und Rahmen) | - verhindern das Eindringen vor Feuchtigkeit |
Modulrahmen | - verleiht dem Module noch mehr Stabilität - schützt die Kanten vor Schäden |
Für Nischenanwendungen - etwa in der dach- und fassadenintegrierten Photovoltaik - wird dieser als Glas-Folien-Modul bezeichnete Aufbau gelegentlich leicht abgewandelt.
An Stelle der Rückseitenfolie wird eine weitere Glasscheibe verbaut, die dem Modul eine höhere mechanische Stabilität verleiht. Das „Glas-Folien-“ wird so zum „Glas-Glas-Modul“.
Es kann auf den versteifenden Metallrahmen verzichten, weshalb es höheren ästhetischen Ansprüchen genügt.
Die Herstellung
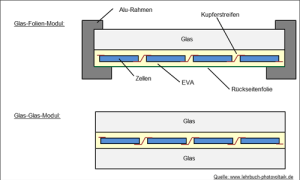
Ob als Glas-Folien- oder Glas-Glas-Modul:
Das richtig aufgebaute kristalline PV-Modul
hält und hält.
Quelle: Lehrbuch-photovoltaik.de
Der marktbeherrschende Modultyp ist und bleibt aber die widerstandsfähige starre Konstruktion des Glas-Folien-Moduls.
Die Schichtfolge ist hierbei nur ein Teil des Aufbau-Puzzles. Für die Qualität ist ebenso entscheidend, wie sorgfältig die Schichten des kristallinen PV-Moduls zusammengefügt werden.
Jeder der großen Hersteller hat hier - wie ein Sternekoch - seine eigenen Zutaten und kleinen Geheimnisse. Im Prinzip wird ein hochwertiges Glas-Folien-Photovoltaikmodul heute aber wie folgt gefertigt.
Aufbau Photovoltaikmodule - die Kernschichten
Im Kern des Glas-Folien-Moduls stecken die in Serie zu Strings zusammengeschlossenen Solarzellen. Für ihre elektrische Verknüpfung sorgen verzinnte, kaum einen Millimeter dicke Kupferstreifen.
Diese Leiterbahnen werden mit den Kontaktstellen der Zellen verlötet, damit sie den erzeugten Solarstrom abtransportieren können.
Anschlussdose & Bypass-Diode
Zusammengeführt werden die Leitungsbänder - und damit der Solarstrom - auf der Rückseite des Photovoltaik-Moduls, in der Anschlussdose.
In ihr befinden sich alle notwendigen Anschlüsse für die Gleichstromkabel, die den Strom zum Anschlusskasten und schließlich zum Wechselrichter weiterleiten.
Die Anschlussdose selbst und die Stecker müssen dabei sowohl elektrisch wie mechanisch besonders robust sein, d.h. unter anderem UV-beständig, schwer entflammbar, doppelt isoliert - und gegen Staub und Strahlwasser geschützt (mindestens IP-Klasse 65, staubdicht und resistent gegen starkes Strahlwasser).
Ebenfalls in der Anschlussdose verbaut werden die Bypass-Dioden. Jeder String bekommt dabei seine eigene Diode, bei den meisten Herstellern sind es zwei bis vier.
Die Gründe, weshalb wenige Bypass-Dioden in der Anschlussdose platziert werden, sind vor allem wirtschaftlicher Natur. Für eine möglichst hohe Verschattungstoleranz wäre nämlich eine Diode pro Solarzelle ideal, da so die Leistungsverluste noch geringer ausfallen würden. Module mit derartig vielen Dioden wurden auch produziert, etwa von Sharp in den 1990er Jahren. Sie haben sich jedoch nicht durchgesetzt, weil sie in der Herstellung zu teuer sind.
Verkapselung
Zur Erhöhung der Standfestig- und Widerstandsfähigkeit wird der Solarzellenverbund fixiert und möglichst dicht eingeschlossen. Für diese Verkapselung wird er in zwei Folien aus dem Verbundkunststoff Ethyl-Vinyl-Acetat (EVA) gepackt.
EVA ist ein transparenter Werkstoff, der auch als Granulat in Zahnpasten oder in Folien und in der Form dämpfender Zwischensohlen bei Schuhen zu finden ist.
In der Modulproduktion werden die beiden EVA-Folien in einem industriellen Laminator auf rund 150° C erhitzt. Das EVA schmilzt, fließt in die Hohlräume zwischen den Zellen und füllt diese aus.
Danach härtet der Kunststoff aus wie Plexiglas - die Verkapselung ist perfekt.
Kristalline Module - die Außenhülle
Abdeckglas & Rückseitenfolie
Für den vollendeten Glas-Folien-Modulaufbau fehlen noch zwei Schichten: Das Glas und die Rückseitenfolie.
Die Glasscheibe schließt den Aufbau auf der lichtzugewandten Seite ab. Sie gewährleistet, dass möglichst viel Licht ins PV-Modul eindringt ("Lichteinkopplung").
Die optischen Eigenschaften des Glases werden durch Aufrauen der Oberfläche und/oder Aufbringen einer zusätzlichen Antireflexschicht verbessert.
Zum anderen dient das Glas als Schutz, vor Staub, Regen, Schnee und auch vor Hagelschlag. Modernes Modulglas hält einem Aufprall von 25 mm großen und 80 km/h schnellen Hagelkörnern stand.
Auf der lichtabgewandten Seite vollendet die Rückseitenfolie den Aufbau. Sie schützt vor Feuchtigkeit und fungiert als elektrischer Isolator.
Die Verbundfolie – nach dem Hersteller oft "Tedlar-Folie", genau wie "Tempo" für Papiertaschentücher - besteht aus Polyvinylfluorid und Polyester, einem äußerst widerstandsfähigen Material.
Hierzu einige Kerndaten: Tedlar-Folien sind nur rund 0,15 bis 0,2 Millimeter dick, wiegen lediglich 200 bis 300 Gramm pro Quadratmeter und weisen eine Dichte von ca. 1.4 Gramm pro Kubikzentimeter auf. Trotzdem haben sie beispielsweise eine Durchschlagsfestigkeit - eine Kennzahl für die Isoliereigenschaft eines Materials - von über 10 Kilovolt: Das ist vergleichbar mit Glas und Emaille.
Zur Erhöhung der Steifigkeit und zum Schutz der Kanten wird das Glas-Folien-Modul abschließend in einen Alu- oder Edelstahlrahmen eingefasst.
Je nach Hersteller wird der Zwischenraum zwischen Glasscheibe und Rahmen mit einem Gummiband oder Silikon aufgefüllt und abgedichtet.
Das rund ein auf eineinhalb Meter große, zwischen 15 und 25 Kilo schwere Modul ist damit fertig und bereit für die Montage in einer PV-Anlage.
Eingehende, aktuelle Beispielrechnungen für Photovoltaikanlagen
finden Sie hier: Photovoltaik lohnt sich!
Wie die Modulproduktion in bewegten Bildern aussieht, zeigt folgendes Video des Herstellers Solon:
Photovoltaikmodule für Ihr Dach? Zum individuellen Preisvergleich:
Aufbau Photovoltaikmodule: die Dünnschichttechnologie
- Verschaltung von Dünnschicht-PV-Modulen
- Dünnschicht-Photovoltaikmodule aus Amorphem Silizium und CdTe
- Dünnschichtmodule aus CIS
Photovoltaikmodule auf Basis von Dünnschichtzellen spielen auf dem Markt weiterhin nur eine Nebenrolle – dies ungeachtet großer Fortschritte etwa beim Wirkungsgrad, der heute unter realen Betriebsbedingungen bis zu 15% erreicht.
Allerdings kann sich dies nicht mit dem Wirkungsgrad von Dickschicht-Modulen messen.
Der Anteil von Dünnschicht-Modulen hat den einstelligen Prozentbereich noch nie verlassen; derzeit liegt er bei rund 9%.
Gleichwohl: Die Dünnschicht-Technologie hat ihre Vorteile - und viele dieser Vorteile sind eng mit dem Aufbau von PV-Modulen und deren Herstellungsprozess verknüpft.
Alle marktrelevanten Dünnschicht-Module bauen auf einer Trägerschicht aus gehärtetem Glas auf, das in der Regel zwischen 1 und 2 mm dick ist.
Auf das Glas wird das Halbleitermaterial der Solarzelle aufgebracht: und zwar in Schichtstärken von wenigen Tausendstel Millimetern (Mikrometern, µm).
Das Material für die Dünnschichtzellen kann amorphes Silizium sein (a-Si), i.e. Silizium mit einer ungeordneten Kristallstruktur; oder eine Kombination aus amorphem und mikrokristallinem Silizium (mikromorphes Silizium bzw. µ-Si), bei der mikroskopisch kleine Partikel aus kristallinem Silizium in die amorphe Halbleiterstruktur eingebracht werden.
Die meisten Dünnschichtmodule - derzeit rund drei Viertel - verwenden Verbindungshalbleiter, für die Halbleiter unterschiedlicher Eigenschaften kombiniert werden. Mit 5% Marktanteil sind Zellen aus Cadmiumtellurid (CdTe) - ein schwarzes, geruchloses Salz des Tellurwasserstoffs - derzeit die dominierende Dünnschicht-Technologie.
Cadmiumtellurid ist vor einigen Jahren etwas ins Gerede gekommen, da es giftig ist und befürchtet wurde, dass es – z.B. bei einem Brand – freigesetzt werden könnte. Inzwischen wurde Entwarnung gegeben: Das Bayrische Landesamt für Umwelt hat in einer Untersuchung festgestellt, dass von PV-Module aus CdTe bei Brand keine Gefahr Gesundheitsgefahr ausgeht.
Daneben haben sich Module mit Zellen aus Kupferkies bzw. Chalkopyrit, ein messing- bis goldgelb oder grünlich schimmerndes Mineral aus der Gruppe der Sulfide, etabliert.
Chemisch exakt wird dieser Verbundstoff als Kupfer-Indium-(Gallium)-Selenid bezeichnet - aus den Anfangsbuchstaben leitet sich die Kurzbezeichnung CIS- bzw. CISG ab.
Unabhängig vom verwendeten Werkstoff ergeben sich aus diesem Aufbau zwei Vorteile:
- A) Die Zell- bzw. Modul-Herstellung benötigt viel weniger Material. Zur Herstellung von kristallinen Zellen genügen heute 5-6 Gramm Silizium pro Watt. Bei Dünnschichtzellen beträgt der Materialaufwand jedoch nur rund ein Zehntel bis ein Hundertstel dessen: Bei CIGS-Zellen sind es rund 0,03 Gramm Indium pro Wp, bei CdTe-Zellen weniger als 0,01 Gramm Tellur.
- B) Außerdem können Dünnschicht-Solarzellen im Zuge der Herstellung gleich zu einem Modul verschaltet werden - es wird ein aufwändiger Arbeitsschritt eingespart. Der Prozess nennt sich integrierte Verschaltung.
Integrierte Verschaltung: Dünnschicht-Modul aus einem Guss

Durch die integrierte Verschaltung kann der Aufbau
von Dünnschicht-Modulen einen kompletten
Fertigungsschritt schwänzen
Quelle: Lehrbuch-photovoltaik.de
Hierfür wird zunächst eine transparente Leiterschicht (TCO von engl. Transparent Conducting Oxid) auf die tragende Glasscheibe aufgedruckt.
Sie besteht aus einer Sauerstoffverbindung, entweder Zinkoxid oder Indium-Zinn-Oxid (ITO).
Diese Schicht ist nur einen halben Mikrometer dick und leitet den in der Zelle erzeugten Solarstrom ab.
Ein hochkonzentrierter Laserstrahl teilt die TCO-Schicht anschließend in Streifen von rund 10 Zentimeter Dicke auf.
Sie entsprechen bereits der gewünschten Größe der Solarzellen, die im nächsten Schritt auf die strukturierte Leiterlage aufgedampft werden (Details dazu im nächsten Abschnitt).
Der Laser gliedert nun auch das Solarzellen-Halbleitermaterial. Auf diese Weise entstehen - anders als bei den quadratischen kristallinen Zellen - einzelne Solarzellenstreifen mit einer Breite von rund 10 Zentimetern.
Die vom Laser ins Zellenmaterial gebrannten Gräben werden abschließend mit einer ca. 0,7 µm dicken, leitenden Schicht aus Silber oder Aluminium aufgefüllt.
Das ist der Rückkontakt, der die Dünnschicht-Zellen in Serie miteinander verschaltet.
Für möglichst geringe elektrische Verluste ist es wichtig, dass die Gräben zwischen den Zellen mehrere Zehntausendstel Millimeter breit sind (siehe Abbildung oben).
Details zur Verschaltung von Photovoltaik-Modulen finden Sie hier
Dieser komprimierte Herstellungsprozess ist - neben dem geringeren Materialaufwand - hauptsächlich dafür verantwortlich, dass Dünnschicht-Module im Schnitt um einige hundert Euro pro Kilowatt günstiger sind als ihre kristallinen Pendants.
Doch kaum ein Vorteil ohne Nachteil. Da eine gesonderte Qualitätsprüfung der Zellen nicht möglich ist, vermindert jedes qualitativ nur minimal minderwertige, inhomogene Solarzellenband die Effektivität des ganzen Moduls.
Eine durchgehend homogene Abscheidung des Halbleitermaterials über die gesamte Modulfläche ist technisch extrem schwierig zu realisieren: Kleine Unterschiede in Qualität und Stärke lassen sich so nicht verhindern - deshalb ist der Wirkungsgrad von Dünnschichtmodulen deutlich geringer als der von kristallinen Paneelen.
Während mono- und polykristalline Module unter Standard-Test-Bedingungen Wirkungsgrade zwischen 15 und 21% bzw. 14 und 18% erreichen, kommen die besten Dünnschichtmodule (CdTe und CIGS) - wie angesprochen - nicht über 14, 15% hinaus.
Unter Laborbedingungen sind für Dünnschichtzellen allerdings schon Spitzenwerte von bis zu 22,5% möglich, die – zurecht – in der Presse gern als Erfolge gefeiert werden, die den Fortschritt der Photovoltaik markieren.
Das ist auch richtig. In der Praxis von Herstellung und Gebrauch sind diese hohen Wirkungsgrade jedoch bisher nicht erreichbar.
Eingesetzt werden Dünnschichtmodule vor allem bei
a. Freiflächenanlagen, bei denen es - anders als bei Hausdachanlagen - nicht auf die effektive Nutzung jedes Quadratzentimeters ankommt, und
b. dort, wo mit wenig direkter Sonneneinstrahlung zu rechnen ist.
Denn bei diffusem Licht sind Dünnschichtmodule effizienter.
Aufbau-Unterschiede zwischen den Dünnschicht-Technologien
Den Aufbau auf einer dünnen Trägerschicht und den gestrafften Produktionsprozess der integrierten Verschaltung haben alle Dünnschichtmodule gemeinsam.
Dennoch gibt es zwei grundlegend unterschiedliche Aufbauarten. Je nachdem, ob die Trägerschicht auf der lichtzu- oder lichtabgewandten Seite des Moduls liegt, unterscheidet man:
- den Superstrat-Aufbau (die Regel bei amorphen, mikromorphen und CdTe-Zellen);
- und den Substrat-Aufbau (für CIS-Zellen).
Dünnschichtmodule im Superstrat-Aufbau
Beim Superstrat-Aufbau liegt die tragende Glasscheibe über den einzelnen Lagen des Dünnschichtmoduls, auf der Seite, von der das Licht einfällt (die Bezeichnung leitet sich ab von lat. super, für dt. über).
Der Aufbau folgt dem Grundmuster der integrierten Verschaltung:
- Glasscheibe
- transparente leitende Schicht (TCO)
- Dünnschichtsolarzelle
- Rückkontakt
Basis ist auch hier eine 1 bis 2 Millimeter dicke, speziell gehärtete Glasscheibe.
Sie ist beim Superstrat-Aufbau aber nicht nur das Trägermaterial für die restlichen Schichten. Das Glas hat darüber hinaus die Aufgabe, durch Aufbau und Oberfläche für einen möglichst günstigen Lichteinfall zu sorgen.
Auf das eisenarme Trägerglas wird eine Antireflexionsschicht aufgebracht, die das Spiegeln des Lichts an der Glasoberfläche verhindert.
Zusätzlich rauen manche Hersteller die Oberfläche auf, um die Lichteinkopplung weiter zu verbessern. Dem selben Ziel dient auch die im nächsten Schritt aufgedruckte, transparente Leiterschicht aus Oxiden: Sie lässt das Licht ungehindert zur Solarzelle passieren.
Beginnend bei der Solarzelle verlangen die verschiedenen Dünnschichttechnologien nach einem jeweils leicht abgewandelten Aufbau.
Der Aufbau von Dickschicht-Photovoltaikmodulen
- Kristalline Photovoltaik-Module: der Aufbau
- Dicksicht-PV-Module: die Herstellung
Wenn heute irgendwo auf der Welt - sei es auf einem Haus, einer Scheune oder einem Solarfeld - eine Photovoltaik-Anlage errichtet wird, dann kommen in 90 von 100 Bauvorhaben kristalline PV-Module zum Einsatz.
Ihr Marktanteil betrug im Jahr 2014 rund 91% (Quelle ISE Fraunhofer, PV-Report [engl.], S. 19).
Dieser Modultyp basiert - wie der Name schon sagt - auf kristallinen Solarzellen, die aus ca. 0,2 Millimeter dicken, rund 15 × 15 Zentimeter großen Silizium-Scheiben (Wafern) bestehen.
Die Bezeichnung „kristallin“ rührt übrigens von der Kristallstruktur der Silizium-Moleküle her. Die besonders hochwertigen Zellen aus monokristallinem Silizium bilden ein vollkommenes Kristallgitter, bei poly- bzw. multikristallinem Silizium ist es immer noch sehr gleichmäßig.
Landläufig werden die kristallinen Solarzellen oft auch Dickschichtzellen genannt: weil sie trotz ihrer geringen Stärke zehn bis hundert Mal dicker sind als Dünnschichtzellen.
Lesen Sie hier, wie Solarzellen aufgebaut sind und funktionieren.
Schicht für Schicht: der Aufbau kristalliner PV-Module im Detail
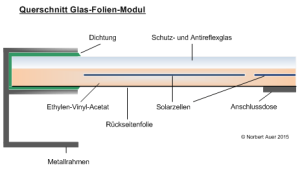
Damit ein Photovoltaikmodul elektrisch
und mechanisch einwandfrei funktioniert,
braucht es zahlreiche Schichten.
© Eigene Darstellung
Dickschicht-Module bestehen im Kern aus kristallinen Solarzellen.
Sie werden in einem von der Modulproduktion gesonderten Fertigungsprozess hergestellt. Das ist ein wesentlicher Unterschied zum Aufbau von Dünnschichtmodulen - ein Unterschied, der einerseits einen höheren technischen Aufwand und damit höhere Kosten verursacht.
Kristalline PV-Module sind nicht zuletzt deshalb pro Kilowatt Leistung ca. 200 bis 500 Euro teurer als Dünnschichtmodule.
Der höhere Herstellungsaufwand hat andererseits auch sein Gutes. Die Zellen lassen sich einzeln auf ihre Qualität prüfen, dabei können minderwertige Wafer aussortiert werden. Das ist einer der Gründe, weshalb kristalline Photovoltaikmodule bis heute einen um 5 bis 10% höheren Wirkungsgrad aufweisen als Dünnschicht-Paneele.
Wie Wafer von hoher Qualität hergestellt werden? Das
erfahren Sie in unserem Artikel über die Silizium-Scheiben.
Erst nach der Sortierung werden rund 30 bis 100 der ausgewählten kristallinen Zellen zum größeren funktionalen Ganzen des kristallinen PV-Moduls zusammengeschlossen.
Dieser gesonderte Fertigungsprozess dient unter anderem auch dazu, die hochsensiblen mikroelektronischen Bauteile, die das Licht in Strom umwandeln, in einen schützenden Kokon aus verschiedenen transparenten Schichten und Materialien einzuweben.
Und so sieht der typische Aufbau eines kristallinen PV-Moduls aus:
Bauteil des PV-Moduls | Funktion des Bauteils |
---|---|
Glasscheibe (Modulvorderseite) | - schützt vor Beschädigung - verbessert die Lichteinkopplung (höherer Wirkungsgrad) |
Solarzellen | - wandeln das Sonnenlicht in Strom um |
Folien aus Ethyl-Vinyl-Acetat (EVA); Ummantelung der Zellen | - die Folieneinbettung fixiert und schützt die Solarzellen |
Rückseitenfolie | - dient als Isolator und Schutz vor Feuchtigkeit |
Anschlussdose | - fasst die Kabel der Solarzellen zentral zusammen, damit die Module leichter miteinander verschaltet werden können - beherbergt die Bypass-Diode(n). Sie verringern Verluste durch teilweise Verschattung |
Dichtungen (zwischen Glasscheibe und Rahmen) | - verhindern das Eindringen vor Feuchtigkeit |
Modulrahmen | - verleiht dem Module noch mehr Stabilität - schützt die Kanten vor Schäden |
Für Nischenanwendungen - etwa in der dach- und fassadenintegrierten Photovoltaik - wird dieser als Glas-Folien-Modul bezeichnete Aufbau gelegentlich leicht abgewandelt.
An Stelle der Rückseitenfolie wird eine weitere Glasscheibe verbaut, die dem Modul eine höhere mechanische Stabilität verleiht. Das „Glas-Folien-“ wird so zum „Glas-Glas-Modul“.
Es kann auf den versteifenden Metallrahmen verzichten, weshalb es höheren ästhetischen Ansprüchen genügt.
Die Herstellung
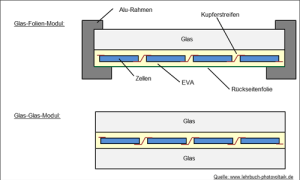
Ob als Glas-Folien- oder Glas-Glas-Modul:
Das richtig aufgebaute kristalline PV-Modul
hält und hält.
Quelle: Lehrbuch-photovoltaik.de
Der marktbeherrschende Modultyp ist und bleibt aber die widerstandsfähige starre Konstruktion des Glas-Folien-Moduls.
Die Schichtfolge ist hierbei nur ein Teil des Aufbau-Puzzles. Für die Qualität ist ebenso entscheidend, wie sorgfältig die Schichten des kristallinen PV-Moduls zusammengefügt werden.
Jeder der großen Hersteller hat hier - wie ein Sternekoch - seine eigenen Zutaten und kleinen Geheimnisse. Im Prinzip wird ein hochwertiges Glas-Folien-Photovoltaikmodul heute aber wie folgt gefertigt.
Aufbau Photovoltaikmodule - die Kernschichten
Im Kern des Glas-Folien-Moduls stecken die in Serie zu Strings zusammengeschlossenen Solarzellen. Für ihre elektrische Verknüpfung sorgen verzinnte, kaum einen Millimeter dicke Kupferstreifen.
Diese Leiterbahnen werden mit den Kontaktstellen der Zellen verlötet, damit sie den erzeugten Solarstrom abtransportieren können.
Anschlussdose & Bypass-Diode
Zusammengeführt werden die Leitungsbänder - und damit der Solarstrom - auf der Rückseite des Photovoltaik-Moduls, in der Anschlussdose.
In ihr befinden sich alle notwendigen Anschlüsse für die Gleichstromkabel, die den Strom zum Anschlusskasten und schließlich zum Wechselrichter weiterleiten.
Die Anschlussdose selbst und die Stecker müssen dabei sowohl elektrisch wie mechanisch besonders robust sein, d.h. unter anderem UV-beständig, schwer entflammbar, doppelt isoliert - und gegen Staub und Strahlwasser geschützt (mindestens IP-Klasse 65, staubdicht und resistent gegen starkes Strahlwasser).
Ebenfalls in der Anschlussdose verbaut werden die Bypass-Dioden. Jeder String bekommt dabei seine eigene Diode, bei den meisten Herstellern sind es zwei bis vier.
Die Gründe, weshalb wenige Bypass-Dioden in der Anschlussdose platziert werden, sind vor allem wirtschaftlicher Natur. Für eine möglichst hohe Verschattungstoleranz wäre nämlich eine Diode pro Solarzelle ideal, da so die Leistungsverluste noch geringer ausfallen würden. Module mit derartig vielen Dioden wurden auch produziert, etwa von Sharp in den 1990er Jahren. Sie haben sich jedoch nicht durchgesetzt, weil sie in der Herstellung zu teuer sind.
Verkapselung
Zur Erhöhung der Standfestig- und Widerstandsfähigkeit wird der Solarzellenverbund fixiert und möglichst dicht eingeschlossen. Für diese Verkapselung wird er in zwei Folien aus dem Verbundkunststoff Ethyl-Vinyl-Acetat (EVA) gepackt.
EVA ist ein transparenter Werkstoff, der auch als Granulat in Zahnpasten oder in Folien und in der Form dämpfender Zwischensohlen bei Schuhen zu finden ist.
In der Modulproduktion werden die beiden EVA-Folien in einem industriellen Laminator auf rund 150° C erhitzt. Das EVA schmilzt, fließt in die Hohlräume zwischen den Zellen und füllt diese aus.
Danach härtet der Kunststoff aus wie Plexiglas - die Verkapselung ist perfekt.
Kristalline Module - die Außenhülle
Abdeckglas & Rückseitenfolie
Für den vollendeten Glas-Folien-Modulaufbau fehlen noch zwei Schichten: Das Glas und die Rückseitenfolie.
Die Glasscheibe schließt den Aufbau auf der lichtzugewandten Seite ab. Sie gewährleistet, dass möglichst viel Licht ins PV-Modul eindringt ("Lichteinkopplung").
Die optischen Eigenschaften des Glases werden durch Aufrauen der Oberfläche und/oder Aufbringen einer zusätzlichen Antireflexschicht verbessert.
Zum anderen dient das Glas als Schutz, vor Staub, Regen, Schnee und auch vor Hagelschlag. Modernes Modulglas hält einem Aufprall von 25 mm großen und 80 km/h schnellen Hagelkörnern stand.
Auf der lichtabgewandten Seite vollendet die Rückseitenfolie den Aufbau. Sie schützt vor Feuchtigkeit und fungiert als elektrischer Isolator.
Die Verbundfolie – nach dem Hersteller oft "Tedlar-Folie", genau wie "Tempo" für Papiertaschentücher - besteht aus Polyvinylfluorid und Polyester, einem äußerst widerstandsfähigen Material.
Hierzu einige Kerndaten: Tedlar-Folien sind nur rund 0,15 bis 0,2 Millimeter dick, wiegen lediglich 200 bis 300 Gramm pro Quadratmeter und weisen eine Dichte von ca. 1.4 Gramm pro Kubikzentimeter auf. Trotzdem haben sie beispielsweise eine Durchschlagsfestigkeit - eine Kennzahl für die Isoliereigenschaft eines Materials - von über 10 Kilovolt: Das ist vergleichbar mit Glas und Emaille.
Zur Erhöhung der Steifigkeit und zum Schutz der Kanten wird das Glas-Folien-Modul abschließend in einen Alu- oder Edelstahlrahmen eingefasst.
Je nach Hersteller wird der Zwischenraum zwischen Glasscheibe und Rahmen mit einem Gummiband oder Silikon aufgefüllt und abgedichtet.
Das rund ein auf eineinhalb Meter große, zwischen 15 und 25 Kilo schwere Modul ist damit fertig und bereit für die Montage in einer PV-Anlage.
Eingehende, aktuelle Beispielrechnungen für Photovoltaikanlagen
finden Sie hier: Photovoltaik lohnt sich!
Wie die Modulproduktion in bewegten Bildern aussieht, zeigt folgendes Video des Herstellers Solon:
Photovoltaikmodule für Ihr Dach? Zum individuellen Preisvergleich:
Aufbau Photovoltaikmodule: die Dünnschichttechnologie
- Verschaltung von Dünnschicht-PV-Modulen
- Dünnschicht-Photovoltaikmodule aus Amorphem Silizium und CdTe
- Dünnschichtmodule aus CIS
Photovoltaikmodule auf Basis von Dünnschichtzellen spielen auf dem Markt weiterhin nur eine Nebenrolle – dies ungeachtet großer Fortschritte etwa beim Wirkungsgrad, der heute unter realen Betriebsbedingungen bis zu 15% erreicht.
Allerdings kann sich dies nicht mit dem Wirkungsgrad von Dickschicht-Modulen messen.
Der Anteil von Dünnschicht-Modulen hat den einstelligen Prozentbereich noch nie verlassen; derzeit liegt er bei rund 9%.
Gleichwohl: Die Dünnschicht-Technologie hat ihre Vorteile - und viele dieser Vorteile sind eng mit dem Aufbau von PV-Modulen und deren Herstellungsprozess verknüpft.
Alle marktrelevanten Dünnschicht-Module bauen auf einer Trägerschicht aus gehärtetem Glas auf, das in der Regel zwischen 1 und 2 mm dick ist.
Auf das Glas wird das Halbleitermaterial der Solarzelle aufgebracht: und zwar in Schichtstärken von wenigen Tausendstel Millimetern (Mikrometern, µm).
Das Material für die Dünnschichtzellen kann amorphes Silizium sein (a-Si), i.e. Silizium mit einer ungeordneten Kristallstruktur; oder eine Kombination aus amorphem und mikrokristallinem Silizium (mikromorphes Silizium bzw. µ-Si), bei der mikroskopisch kleine Partikel aus kristallinem Silizium in die amorphe Halbleiterstruktur eingebracht werden.
Die meisten Dünnschichtmodule - derzeit rund drei Viertel - verwenden Verbindungshalbleiter, für die Halbleiter unterschiedlicher Eigenschaften kombiniert werden. Mit 5% Marktanteil sind Zellen aus Cadmiumtellurid (CdTe) - ein schwarzes, geruchloses Salz des Tellurwasserstoffs - derzeit die dominierende Dünnschicht-Technologie.
Cadmiumtellurid ist vor einigen Jahren etwas ins Gerede gekommen, da es giftig ist und befürchtet wurde, dass es – z.B. bei einem Brand – freigesetzt werden könnte. Inzwischen wurde Entwarnung gegeben: Das Bayrische Landesamt für Umwelt hat in einer Untersuchung festgestellt, dass von PV-Module aus CdTe bei Brand keine Gefahr Gesundheitsgefahr ausgeht.
Daneben haben sich Module mit Zellen aus Kupferkies bzw. Chalkopyrit, ein messing- bis goldgelb oder grünlich schimmerndes Mineral aus der Gruppe der Sulfide, etabliert.
Chemisch exakt wird dieser Verbundstoff als Kupfer-Indium-(Gallium)-Selenid bezeichnet - aus den Anfangsbuchstaben leitet sich die Kurzbezeichnung CIS- bzw. CISG ab.
Unabhängig vom verwendeten Werkstoff ergeben sich aus diesem Aufbau zwei Vorteile:
- A) Die Zell- bzw. Modul-Herstellung benötigt viel weniger Material. Zur Herstellung von kristallinen Zellen genügen heute 5-6 Gramm Silizium pro Watt. Bei Dünnschichtzellen beträgt der Materialaufwand jedoch nur rund ein Zehntel bis ein Hundertstel dessen: Bei CIGS-Zellen sind es rund 0,03 Gramm Indium pro Wp, bei CdTe-Zellen weniger als 0,01 Gramm Tellur.
- B) Außerdem können Dünnschicht-Solarzellen im Zuge der Herstellung gleich zu einem Modul verschaltet werden - es wird ein aufwändiger Arbeitsschritt eingespart. Der Prozess nennt sich integrierte Verschaltung.
Integrierte Verschaltung: Dünnschicht-Modul aus einem Guss

Durch die integrierte Verschaltung kann der Aufbau
von Dünnschicht-Modulen einen kompletten
Fertigungsschritt schwänzen
Quelle: Lehrbuch-photovoltaik.de
Hierfür wird zunächst eine transparente Leiterschicht (TCO von engl. Transparent Conducting Oxid) auf die tragende Glasscheibe aufgedruckt.
Sie besteht aus einer Sauerstoffverbindung, entweder Zinkoxid oder Indium-Zinn-Oxid (ITO).
Diese Schicht ist nur einen halben Mikrometer dick und leitet den in der Zelle erzeugten Solarstrom ab.
Ein hochkonzentrierter Laserstrahl teilt die TCO-Schicht anschließend in Streifen von rund 10 Zentimeter Dicke auf.
Sie entsprechen bereits der gewünschten Größe der Solarzellen, die im nächsten Schritt auf die strukturierte Leiterlage aufgedampft werden (Details dazu im nächsten Abschnitt).
Der Laser gliedert nun auch das Solarzellen-Halbleitermaterial. Auf diese Weise entstehen - anders als bei den quadratischen kristallinen Zellen - einzelne Solarzellenstreifen mit einer Breite von rund 10 Zentimetern.
Die vom Laser ins Zellenmaterial gebrannten Gräben werden abschließend mit einer ca. 0,7 µm dicken, leitenden Schicht aus Silber oder Aluminium aufgefüllt.
Das ist der Rückkontakt, der die Dünnschicht-Zellen in Serie miteinander verschaltet.
Für möglichst geringe elektrische Verluste ist es wichtig, dass die Gräben zwischen den Zellen mehrere Zehntausendstel Millimeter breit sind (siehe Abbildung oben).
Details zur Verschaltung von Photovoltaik-Modulen finden Sie hier
Vor- & Nachteile
Dieser komprimierte Herstellungsprozess ist - neben dem geringeren Materialaufwand - hauptsächlich dafür verantwortlich, dass Dünnschicht-Module im Schnitt um einige hundert Euro pro Kilowatt günstiger sind als ihre kristallinen Pendants.
Doch kaum ein Vorteil ohne Nachteil. Da eine gesonderte Qualitätsprüfung der Zellen nicht möglich ist, vermindert jedes qualitativ nur minimal minderwertige, inhomogene Solarzellenband die Effektivität des ganzen Moduls.
Eine durchgehend homogene Abscheidung des Halbleitermaterials über die gesamte Modulfläche ist technisch extrem schwierig zu realisieren: Kleine Unterschiede in Qualität und Stärke lassen sich so nicht verhindern - deshalb ist der Wirkungsgrad von Dünnschichtmodulen deutlich geringer als der von kristallinen Paneelen.
Während mono- und polykristalline Module unter Standard-Test-Bedingungen Wirkungsgrade zwischen 15 und 21% bzw. 14 und 18% erreichen, kommen die besten Dünnschichtmodule (CdTe und CIGS) - wie angesprochen - nicht über 14, 15% hinaus.
Unter Laborbedingungen sind für Dünnschichtzellen allerdings schon Spitzenwerte von bis zu 22,5% möglich, die – zurecht – in der Presse gern als Erfolge gefeiert werden, die den Fortschritt der Photovoltaik markieren.
Das ist auch richtig. In der Praxis von Herstellung und Gebrauch sind diese hohen Wirkungsgrade jedoch bisher nicht erreichbar.
Eingesetzt werden Dünnschichtmodule vor allem bei
a. Freiflächenanlagen, bei denen es - anders als bei Hausdachanlagen - nicht auf die effektive Nutzung jedes Quadratzentimeters ankommt, und
b. dort, wo mit wenig direkter Sonneneinstrahlung zu rechnen ist.
Denn bei diffusem Licht sind Dünnschichtmodule effizienter.
Aufbau-Unterschiede zwischen den Dünnschicht-Technologien
Den Aufbau auf einer dünnen Trägerschicht und den gestrafften Produktionsprozess der integrierten Verschaltung haben alle Dünnschichtmodule gemeinsam.
Dennoch gibt es zwei grundlegend unterschiedliche Aufbauarten. Je nachdem, ob die Trägerschicht auf der lichtzu- oder lichtabgewandten Seite des Moduls liegt, unterscheidet man:
- den Superstrat-Aufbau (die Regel bei amorphen, mikromorphen und CdTe-Zellen);
- und den Substrat-Aufbau (für CIS-Zellen).
Dünnschichtmodule im Superstrat-Aufbau
Beim Superstrat-Aufbau liegt die tragende Glasscheibe über den einzelnen Lagen des Dünnschichtmoduls, auf der Seite, von der das Licht einfällt (die Bezeichnung leitet sich ab von lat. super, für dt. über).
Der Aufbau folgt dem Grundmuster der integrierten Verschaltung:
- Glasscheibe
- transparente leitende Schicht (TCO)
- Dünnschichtsolarzelle
- Rückkontakt
Basis ist auch hier eine 1 bis 2 Millimeter dicke, speziell gehärtete Glasscheibe.
Sie ist beim Superstrat-Aufbau aber nicht nur das Trägermaterial für die restlichen Schichten. Das Glas hat darüber hinaus die Aufgabe, durch Aufbau und Oberfläche für einen möglichst günstigen Lichteinfall zu sorgen.
Auf das eisenarme Trägerglas wird eine Antireflexionsschicht aufgebracht, die das Spiegeln des Lichts an der Glasoberfläche verhindert.
Zusätzlich rauen manche Hersteller die Oberfläche auf, um die Lichteinkopplung weiter zu verbessern. Dem selben Ziel dient auch die im nächsten Schritt aufgedruckte, transparente Leiterschicht aus Oxiden: Sie lässt das Licht ungehindert zur Solarzelle passieren.
Beginnend bei der Solarzelle verlangen die verschiedenen Dünnschichttechnologien nach einem jeweils leicht abgewandelten Aufbau.
Der Aufbau von Dickschicht-Photovoltaikmodulen
- Kristalline Photovoltaik-Module: der Aufbau
- Dicksicht-PV-Module: die Herstellung
Wenn heute irgendwo auf der Welt - sei es auf einem Haus, einer Scheune oder einem Solarfeld - eine Photovoltaik-Anlage errichtet wird, dann kommen in 90 von 100 Bauvorhaben kristalline PV-Module zum Einsatz.
Ihr Marktanteil betrug im Jahr 2014 rund 91% (Quelle ISE Fraunhofer, PV-Report [engl.], S. 19).
Dieser Modultyp basiert - wie der Name schon sagt - auf kristallinen Solarzellen, die aus ca. 0,2 Millimeter dicken, rund 15 × 15 Zentimeter großen Silizium-Scheiben (Wafern) bestehen.
Die Bezeichnung „kristallin“ rührt übrigens von der Kristallstruktur der Silizium-Moleküle her. Die besonders hochwertigen Zellen aus monokristallinem Silizium bilden ein vollkommenes Kristallgitter, bei poly- bzw. multikristallinem Silizium ist es immer noch sehr gleichmäßig.
Landläufig werden die kristallinen Solarzellen oft auch Dickschichtzellen genannt: weil sie trotz ihrer geringen Stärke zehn bis hundert Mal dicker sind als Dünnschichtzellen.
Lesen Sie hier, wie Solarzellen aufgebaut sind und funktionieren.
Schicht für Schicht: der Aufbau kristalliner PV-Module im Detail
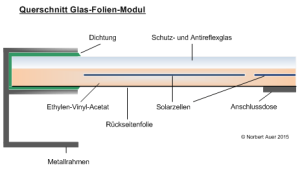
Damit ein Photovoltaikmodul elektrisch
und mechanisch einwandfrei funktioniert,
braucht es zahlreiche Schichten.
© Eigene Darstellung
Dickschicht-Module bestehen im Kern aus kristallinen Solarzellen.
Sie werden in einem von der Modulproduktion gesonderten Fertigungsprozess hergestellt. Das ist ein wesentlicher Unterschied zum Aufbau von Dünnschichtmodulen - ein Unterschied, der einerseits einen höheren technischen Aufwand und damit höhere Kosten verursacht.
Kristalline PV-Module sind nicht zuletzt deshalb pro Kilowatt Leistung ca. 200 bis 500 Euro teurer als Dünnschichtmodule.
Der höhere Herstellungsaufwand hat andererseits auch sein Gutes. Die Zellen lassen sich einzeln auf ihre Qualität prüfen, dabei können minderwertige Wafer aussortiert werden. Das ist einer der Gründe, weshalb kristalline Photovoltaikmodule bis heute einen um 5 bis 10% höheren Wirkungsgrad aufweisen als Dünnschicht-Paneele.
Wie Wafer von hoher Qualität hergestellt werden? Das
erfahren Sie in unserem Artikel über die Silizium-Scheiben.
Erst nach der Sortierung werden rund 30 bis 100 der ausgewählten kristallinen Zellen zum größeren funktionalen Ganzen des kristallinen PV-Moduls zusammengeschlossen.
Dieser gesonderte Fertigungsprozess dient unter anderem auch dazu, die hochsensiblen mikroelektronischen Bauteile, die das Licht in Strom umwandeln, in einen schützenden Kokon aus verschiedenen transparenten Schichten und Materialien einzuweben.
Und so sieht der typische Aufbau eines kristallinen PV-Moduls aus:
Bauteil des PV-Moduls | Funktion des Bauteils |
---|---|
Glasscheibe (Modulvorderseite) | - schützt vor Beschädigung - verbessert die Lichteinkopplung (höherer Wirkungsgrad) |
Solarzellen | - wandeln das Sonnenlicht in Strom um |
Folien aus Ethyl-Vinyl-Acetat (EVA); Ummantelung der Zellen | - die Folieneinbettung fixiert und schützt die Solarzellen |
Rückseitenfolie | - dient als Isolator und Schutz vor Feuchtigkeit |
Anschlussdose | - fasst die Kabel der Solarzellen zentral zusammen, damit die Module leichter miteinander verschaltet werden können - beherbergt die Bypass-Diode(n). Sie verringern Verluste durch teilweise Verschattung |
Dichtungen (zwischen Glasscheibe und Rahmen) | - verhindern das Eindringen vor Feuchtigkeit |
Modulrahmen | - verleiht dem Module noch mehr Stabilität - schützt die Kanten vor Schäden |
Für Nischenanwendungen - etwa in der dach- und fassadenintegrierten Photovoltaik - wird dieser als Glas-Folien-Modul bezeichnete Aufbau gelegentlich leicht abgewandelt.
An Stelle der Rückseitenfolie wird eine weitere Glasscheibe verbaut, die dem Modul eine höhere mechanische Stabilität verleiht. Das „Glas-Folien-“ wird so zum „Glas-Glas-Modul“.
Es kann auf den versteifenden Metallrahmen verzichten, weshalb es höheren ästhetischen Ansprüchen genügt.
Die Herstellung
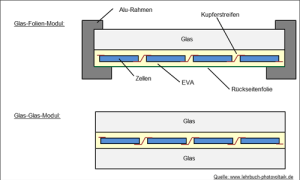
Ob als Glas-Folien- oder Glas-Glas-Modul:
Das richtig aufgebaute kristalline PV-Modul
hält und hält.
Quelle: Lehrbuch-photovoltaik.de
Der marktbeherrschende Modultyp ist und bleibt aber die widerstandsfähige starre Konstruktion des Glas-Folien-Moduls.
Die Schichtfolge ist hierbei nur ein Teil des Aufbau-Puzzles. Für die Qualität ist ebenso entscheidend, wie sorgfältig die Schichten des kristallinen PV-Moduls zusammengefügt werden.
Jeder der großen Hersteller hat hier - wie ein Sternekoch - seine eigenen Zutaten und kleinen Geheimnisse. Im Prinzip wird ein hochwertiges Glas-Folien-Photovoltaikmodul heute aber wie folgt gefertigt.
Aufbau Photovoltaikmodule - die Kernschichten
Im Kern des Glas-Folien-Moduls stecken die in Serie zu Strings zusammengeschlossenen Solarzellen. Für ihre elektrische Verknüpfung sorgen verzinnte, kaum einen Millimeter dicke Kupferstreifen.
Diese Leiterbahnen werden mit den Kontaktstellen der Zellen verlötet, damit sie den erzeugten Solarstrom abtransportieren können.
Anschlussdose & Bypass-Diode
Zusammengeführt werden die Leitungsbänder - und damit der Solarstrom - auf der Rückseite des Photovoltaik-Moduls, in der Anschlussdose.
In ihr befinden sich alle notwendigen Anschlüsse für die Gleichstromkabel, die den Strom zum Anschlusskasten und schließlich zum Wechselrichter weiterleiten.
Die Anschlussdose selbst und die Stecker müssen dabei sowohl elektrisch wie mechanisch besonders robust sein, d.h. unter anderem UV-beständig, schwer entflammbar, doppelt isoliert - und gegen Staub und Strahlwasser geschützt (mindestens IP-Klasse 65, staubdicht und resistent gegen starkes Strahlwasser).
Ebenfalls in der Anschlussdose verbaut werden die Bypass-Dioden. Jeder String bekommt dabei seine eigene Diode, bei den meisten Herstellern sind es zwei bis vier.
Die Gründe, weshalb wenige Bypass-Dioden in der Anschlussdose platziert werden, sind vor allem wirtschaftlicher Natur. Für eine möglichst hohe Verschattungstoleranz wäre nämlich eine Diode pro Solarzelle ideal, da so die Leistungsverluste noch geringer ausfallen würden. Module mit derartig vielen Dioden wurden auch produziert, etwa von Sharp in den 1990er Jahren. Sie haben sich jedoch nicht durchgesetzt, weil sie in der Herstellung zu teuer sind.
Verkapselung
Zur Erhöhung der Standfestig- und Widerstandsfähigkeit wird der Solarzellenverbund fixiert und möglichst dicht eingeschlossen. Für diese Verkapselung wird er in zwei Folien aus dem Verbundkunststoff Ethyl-Vinyl-Acetat (EVA) gepackt.
EVA ist ein transparenter Werkstoff, der auch als Granulat in Zahnpasten oder in Folien und in der Form dämpfender Zwischensohlen bei Schuhen zu finden ist.
In der Modulproduktion werden die beiden EVA-Folien in einem industriellen Laminator auf rund 150° C erhitzt. Das EVA schmilzt, fließt in die Hohlräume zwischen den Zellen und füllt diese aus.
Danach härtet der Kunststoff aus wie Plexiglas - die Verkapselung ist perfekt.
Kristalline Module - die Außenhülle
Abdeckglas & Rückseitenfolie
Für den vollendeten Glas-Folien-Modulaufbau fehlen noch zwei Schichten: Das Glas und die Rückseitenfolie.
Die Glasscheibe schließt den Aufbau auf der lichtzugewandten Seite ab. Sie gewährleistet, dass möglichst viel Licht ins PV-Modul eindringt ("Lichteinkopplung").
Die optischen Eigenschaften des Glases werden durch Aufrauen der Oberfläche und/oder Aufbringen einer zusätzlichen Antireflexschicht verbessert.
Zum anderen dient das Glas als Schutz, vor Staub, Regen, Schnee und auch vor Hagelschlag. Modernes Modulglas hält einem Aufprall von 25 mm großen und 80 km/h schnellen Hagelkörnern stand.
Auf der lichtabgewandten Seite vollendet die Rückseitenfolie den Aufbau. Sie schützt vor Feuchtigkeit und fungiert als elektrischer Isolator.
Die Verbundfolie – nach dem Hersteller oft "Tedlar-Folie", genau wie "Tempo" für Papiertaschentücher - besteht aus Polyvinylfluorid und Polyester, einem äußerst widerstandsfähigen Material.
Hierzu einige Kerndaten: Tedlar-Folien sind nur rund 0,15 bis 0,2 Millimeter dick, wiegen lediglich 200 bis 300 Gramm pro Quadratmeter und weisen eine Dichte von ca. 1.4 Gramm pro Kubikzentimeter auf. Trotzdem haben sie beispielsweise eine Durchschlagsfestigkeit - eine Kennzahl für die Isoliereigenschaft eines Materials - von über 10 Kilovolt: Das ist vergleichbar mit Glas und Emaille.
Zur Erhöhung der Steifigkeit und zum Schutz der Kanten wird das Glas-Folien-Modul abschließend in einen Alu- oder Edelstahlrahmen eingefasst.
Je nach Hersteller wird der Zwischenraum zwischen Glasscheibe und Rahmen mit einem Gummiband oder Silikon aufgefüllt und abgedichtet.
Das rund ein auf eineinhalb Meter große, zwischen 15 und 25 Kilo schwere Modul ist damit fertig und bereit für die Montage in einer PV-Anlage.
Eingehende, aktuelle Beispielrechnungen für Photovoltaikanlagen
finden Sie hier: Photovoltaik lohnt sich!
Wie die Modulproduktion in bewegten Bildern aussieht, zeigt folgendes Video des Herstellers Solon:
Photovoltaikmodule für Ihr Dach? Zum individuellen Preisvergleich:
Aufbau Photovoltaikmodule: die Dünnschichttechnologie
- Verschaltung von Dünnschicht-PV-Modulen
- Dünnschicht-Photovoltaikmodule aus Amorphem Silizium und CdTe
- Dünnschichtmodule aus CIS
Photovoltaikmodule auf Basis von Dünnschichtzellen spielen auf dem Markt weiterhin nur eine Nebenrolle – dies ungeachtet großer Fortschritte etwa beim Wirkungsgrad, der heute unter realen Betriebsbedingungen bis zu 15% erreicht.
Allerdings kann sich dies nicht mit dem Wirkungsgrad von Dickschicht-Modulen messen.
Der Anteil von Dünnschicht-Modulen hat den einstelligen Prozentbereich noch nie verlassen; derzeit liegt er bei rund 9%.
Gleichwohl: Die Dünnschicht-Technologie hat ihre Vorteile - und viele dieser Vorteile sind eng mit dem Aufbau von PV-Modulen und deren Herstellungsprozess verknüpft.
Alle marktrelevanten Dünnschicht-Module bauen auf einer Trägerschicht aus gehärtetem Glas auf, das in der Regel zwischen 1 und 2 mm dick ist.
Auf das Glas wird das Halbleitermaterial der Solarzelle aufgebracht: und zwar in Schichtstärken von wenigen Tausendstel Millimetern (Mikrometern, µm).
Das Material für die Dünnschichtzellen kann amorphes Silizium sein (a-Si), i.e. Silizium mit einer ungeordneten Kristallstruktur; oder eine Kombination aus amorphem und mikrokristallinem Silizium (mikromorphes Silizium bzw. µ-Si), bei der mikroskopisch kleine Partikel aus kristallinem Silizium in die amorphe Halbleiterstruktur eingebracht werden.
Die meisten Dünnschichtmodule - derzeit rund drei Viertel - verwenden Verbindungshalbleiter, für die Halbleiter unterschiedlicher Eigenschaften kombiniert werden. Mit 5% Marktanteil sind Zellen aus Cadmiumtellurid (CdTe) - ein schwarzes, geruchloses Salz des Tellurwasserstoffs - derzeit die dominierende Dünnschicht-Technologie.
Cadmiumtellurid ist vor einigen Jahren etwas ins Gerede gekommen, da es giftig ist und befürchtet wurde, dass es – z.B. bei einem Brand – freigesetzt werden könnte. Inzwischen wurde Entwarnung gegeben: Das Bayrische Landesamt für Umwelt hat in einer Untersuchung festgestellt, dass von PV-Module aus CdTe bei Brand keine Gefahr Gesundheitsgefahr ausgeht.
Daneben haben sich Module mit Zellen aus Kupferkies bzw. Chalkopyrit, ein messing- bis goldgelb oder grünlich schimmerndes Mineral aus der Gruppe der Sulfide, etabliert.
Chemisch exakt wird dieser Verbundstoff als Kupfer-Indium-(Gallium)-Selenid bezeichnet - aus den Anfangsbuchstaben leitet sich die Kurzbezeichnung CIS- bzw. CISG ab.
Unabhängig vom verwendeten Werkstoff ergeben sich aus diesem Aufbau zwei Vorteile:
- A) Die Zell- bzw. Modul-Herstellung benötigt viel weniger Material. Zur Herstellung von kristallinen Zellen genügen heute 5-6 Gramm Silizium pro Watt. Bei Dünnschichtzellen beträgt der Materialaufwand jedoch nur rund ein Zehntel bis ein Hundertstel dessen: Bei CIGS-Zellen sind es rund 0,03 Gramm Indium pro Wp, bei CdTe-Zellen weniger als 0,01 Gramm Tellur.
- B) Außerdem können Dünnschicht-Solarzellen im Zuge der Herstellung gleich zu einem Modul verschaltet werden - es wird ein aufwändiger Arbeitsschritt eingespart. Der Prozess nennt sich integrierte Verschaltung.
Integrierte Verschaltung: Dünnschicht-Modul aus einem Guss

Durch die integrierte Verschaltung kann der Aufbau
von Dünnschicht-Modulen einen kompletten
Fertigungsschritt schwänzen
Quelle: Lehrbuch-photovoltaik.de
Hierfür wird zunächst eine transparente Leiterschicht (TCO von engl. Transparent Conducting Oxid) auf die tragende Glasscheibe aufgedruckt.
Sie besteht aus einer Sauerstoffverbindung, entweder Zinkoxid oder Indium-Zinn-Oxid (ITO).
Diese Schicht ist nur einen halben Mikrometer dick und leitet den in der Zelle erzeugten Solarstrom ab.
Ein hochkonzentrierter Laserstrahl teilt die TCO-Schicht anschließend in Streifen von rund 10 Zentimeter Dicke auf.
Sie entsprechen bereits der gewünschten Größe der Solarzellen, die im nächsten Schritt auf die strukturierte Leiterlage aufgedampft werden (Details dazu im nächsten Abschnitt).
Der Laser gliedert nun auch das Solarzellen-Halbleitermaterial. Auf diese Weise entstehen - anders als bei den quadratischen kristallinen Zellen - einzelne Solarzellenstreifen mit einer Breite von rund 10 Zentimetern.
Die vom Laser ins Zellenmaterial gebrannten Gräben werden abschließend mit einer ca. 0,7 µm dicken, leitenden Schicht aus Silber oder Aluminium aufgefüllt.
Das ist der Rückkontakt, der die Dünnschicht-Zellen in Serie miteinander verschaltet.
Für möglichst geringe elektrische Verluste ist es wichtig, dass die Gräben zwischen den Zellen mehrere Zehntausendstel Millimeter breit sind (siehe Abbildung oben).
Details zur Verschaltung von Photovoltaik-Modulen finden Sie hier
Vor- & Nachteile
Dieser komprimierte Herstellungsprozess ist - neben dem geringeren Materialaufwand - hauptsächlich dafür verantwortlich, dass Dünnschicht-Module im Schnitt um einige hundert Euro pro Kilowatt günstiger sind als ihre kristallinen Pendants.
Doch kaum ein Vorteil ohne Nachteil. Da eine gesonderte Qualitätsprüfung der Zellen nicht möglich ist, vermindert jedes qualitativ nur minimal minderwertige, inhomogene Solarzellenband die Effektivität des ganzen Moduls.
Eine durchgehend homogene Abscheidung des Halbleitermaterials über die gesamte Modulfläche ist technisch extrem schwierig zu realisieren: Kleine Unterschiede in Qualität und Stärke lassen sich so nicht verhindern - deshalb ist der Wirkungsgrad von Dünnschichtmodulen deutlich geringer als der von kristallinen Paneelen.
Während mono- und polykristalline Module unter Standard-Test-Bedingungen Wirkungsgrade zwischen 15 und 21% bzw. 14 und 18% erreichen, kommen die besten Dünnschichtmodule (CdTe und CIGS) - wie angesprochen - nicht über 14, 15% hinaus.
Unter Laborbedingungen sind für Dünnschichtzellen allerdings schon Spitzenwerte von bis zu 22,5% möglich, die – zurecht – in der Presse gern als Erfolge gefeiert werden, die den Fortschritt der Photovoltaik markieren.
Das ist auch richtig. In der Praxis von Herstellung und Gebrauch sind diese hohen Wirkungsgrade jedoch bisher nicht erreichbar.
Eingesetzt werden Dünnschichtmodule vor allem bei
a. Freiflächenanlagen, bei denen es - anders als bei Hausdachanlagen - nicht auf die effektive Nutzung jedes Quadratzentimeters ankommt, und
b. dort, wo mit wenig direkter Sonneneinstrahlung zu rechnen ist.
Denn bei diffusem Licht sind Dünnschichtmodule effizienter.
Aufbau-Unterschiede zwischen den Dünnschicht-Technologien
Den Aufbau auf einer dünnen Trägerschicht und den gestrafften Produktionsprozess der integrierten Verschaltung haben alle Dünnschichtmodule gemeinsam.
Dennoch gibt es zwei grundlegend unterschiedliche Aufbauarten. Je nachdem, ob die Trägerschicht auf der lichtzu- oder lichtabgewandten Seite des Moduls liegt, unterscheidet man:
- den Superstrat-Aufbau (die Regel bei amorphen, mikromorphen und CdTe-Zellen);
- und den Substrat-Aufbau (für CIS-Zellen).
Dünnschichtmodule im Superstrat-Aufbau
Beim Superstrat-Aufbau liegt die tragende Glasscheibe über den einzelnen Lagen des Dünnschichtmoduls, auf der Seite, von der das Licht einfällt (die Bezeichnung leitet sich ab von lat. super, für dt. über).
Der Aufbau folgt dem Grundmuster der integrierten Verschaltung:
- Glasscheibe
- transparente leitende Schicht (TCO)
- Dünnschichtsolarzelle
- Rückkontakt
Basis ist auch hier eine 1 bis 2 Millimeter dicke, speziell gehärtete Glasscheibe.
Sie ist beim Superstrat-Aufbau aber nicht nur das Trägermaterial für die restlichen Schichten. Das Glas hat darüber hinaus die Aufgabe, durch Aufbau und Oberfläche für einen möglichst günstigen Lichteinfall zu sorgen.
Auf das eisenarme Trägerglas wird eine Antireflexionsschicht aufgebracht, die das Spiegeln des Lichts an der Glasoberfläche verhindert.
Zusätzlich rauen manche Hersteller die Oberfläche auf, um die Lichteinkopplung weiter zu verbessern. Dem selben Ziel dient auch die im nächsten Schritt aufgedruckte, transparente Leiterschicht aus Oxiden: Sie lässt das Licht ungehindert zur Solarzelle passieren.
Beginnend bei der Solarzelle verlangen die verschiedenen Dünnschichttechnologien nach einem jeweils leicht abgewandelten Aufbau.
Amorphes Silizium:
Die einzelnen Schichten des amorphen Siliziums werden mit Hilfe der plasmaunterstützten Gasphasenabscheidung (PECVD-Verfahren) bei rund 200 Grad aufgedampft.
Als erstes lagert sich positiv-dotiertes Silizium auf der TCO-Schicht ab, danach folgt undotiertes (intrinsisches) und schließlich negativ-dotiertes Silizium. Aufgrund der Schichtenfolge positiv – intrinsich – negativ sprechen Experten von der pin-Zelle.
Da das aufgedampfte Silizium keine geordnete Struktur aufweist, wird es als amorph (d.h. „unstrukturiert“) bezeichnet. Die vielen offenen Bindungen des Materials sind auch der Grund für den relativ schlechten Wirkungsgrad (7-8%).
Die intrinsische Schicht ist 0,2 bis 0,4 µm dick und absorbiert den Großteil des Lichts. Die positiv und negativ dotierten Lagen messen hingegen nur rund 10 Nanometer, d.h. 10 Millionstel Millimeter – für die Funktion der Solarzelle sind sie aber ebenso entscheidend: Erst durch den pn-Übergang zwischen der positiv- und negativ-dotierten Schicht können die vom Licht erzeugten Elektronen in nutzbaren Strom verwandelt werden.
Der Typische Aufbau von Dünnschichtzellen aus amorphem Silizium beträgt damit 2 bis 4 µm.
Mikromorphes Silizium: Eine relativ junge, vielversprechende Variante dieser Technologie sind Dünnschichtzellen aus mikromorphem Silizium. Hergestellt werden sie ebenfalls im PECVD-Verfahren: Auf eine rund 0,25 µm dicke amorphe Siliziumschicht dampft man hier aber mikrokristalline Siliziumpartikel auf, die deutlich kleiner als 1 Mikrometer sind.
Sie finden sich im amorphen Silizium zu kleinen Konglomeraten zusammen und bilden gemeinsam eine 1 bis 4 Mikrometer starke mikromorphe Solarzelle. Der Vorteil: Weil sich mikrokristallines wie kristallines Silizium verhält, können diese Zellen das Sonnenspektrum besser nutzen und so einen signifikant höheren Wirkungsgrad erzielen (derzeit rund 12%).
CdTe-Halbleiter:
Cadmiumtellurid hat unter anderem den Vorteil, dass es – durch simple thermische Verdampfung bei rund 500 Grad – einfach und sehr gleichmäßig auf ein Substrat abgeschieden werden kann.
Einziges Problem: Cadmiumtellurid lässt sich nur schwer negativ dotieren. Deshalb folgt auf die TCO-Schicht zunächst eine hauchdünne, rund 0,15 µm dicke Lage aus Cadmium-Sulfid: sie ist der n-dotierte Halbleiter.
Erst danach kommt die ca. 3 µm dicke p-dotierte Schicht aus CdTe, durch die der wichtige pn-Übergang entsteht; noch vor einem Jahrzehnt waren Schichtstärken von 5 bis 10 Mikrometern die Regel.
Die abschließenden Schichten von Dünnschichtmodulen im Superstrat-Aufbau sind schließlich wieder für alle Technologien identisch.
Auf das jeweilige Halbleitermaterial der Dünnschichtzelle kommt die ca. 0,7 µm dicke Rückkontakt-Lage aus Aluminium (Silber bei mikromorphen Zellen). Sie schließt – wenn die PV-Module einmal zu einer PV-Anlage verschaltet sind – den Stromkreis und lässt die aus dem Licht gewonnene elektrische Energie fließen. Verkapselt, sprich vor Umwelteinflüssen geschützt, werden die Dünnschicht-Module wie Glas-Folien-Module – durch eine EVA-Folien, auf der eine Rückscheibe auflaminiert wird.
Ein Metallrahmen zur Versteifung ist meist nicht notwendig: Denn die fertigen Module werden bei der Montage in einen vorbereiteten Alu- oder Edelstahlrahmen eingeklemmt.
Amorphes Silizium:
Die einzelnen Schichten des amorphen Siliziums werden mit Hilfe der plasmaunterstützten Gasphasenabscheidung (PECVD-Verfahren) bei rund 200 Grad aufgedampft.
Als erstes lagert sich positiv-dotiertes Silizium auf der TCO-Schicht ab, danach folgt undotiertes (intrinsisches) und schließlich negativ-dotiertes Silizium. Aufgrund der Schichtenfolge positiv – intrinsich – negativ sprechen Experten von der pin-Zelle.
Da das aufgedampfte Silizium keine geordnete Struktur aufweist, wird es als amorph (d.h. „unstrukturiert“) bezeichnet. Die vielen offenen Bindungen des Materials sind auch der Grund für den relativ schlechten Wirkungsgrad (7-8%).
Die intrinsische Schicht ist 0,2 bis 0,4 µm dick und absorbiert den Großteil des Lichts. Die positiv und negativ dotierten Lagen messen hingegen nur rund 10 Nanometer, d.h. 10 Millionstel Millimeter – für die Funktion der Solarzelle sind sie aber ebenso entscheidend: Erst durch den pn-Übergang zwischen der positiv- und negativ-dotierten Schicht können die vom Licht erzeugten Elektronen in nutzbaren Strom verwandelt werden.
Der Typische Aufbau von Dünnschichtzellen aus amorphem Silizium beträgt damit 2 bis 4 µm.
Mikromorphes Silizium: Eine relativ junge, vielversprechende Variante dieser Technologie sind Dünnschichtzellen aus mikromorphem Silizium. Hergestellt werden sie ebenfalls im PECVD-Verfahren: Auf eine rund 0,25 µm dicke amorphe Siliziumschicht dampft man hier aber mikrokristalline Siliziumpartikel auf, die deutlich kleiner als 1 Mikrometer sind.
Sie finden sich im amorphen Silizium zu kleinen Konglomeraten zusammen und bilden gemeinsam eine 1 bis 4 Mikrometer starke mikromorphe Solarzelle. Der Vorteil: Weil sich mikrokristallines wie kristallines Silizium verhält, können diese Zellen das Sonnenspektrum besser nutzen und so einen signifikant höheren Wirkungsgrad erzielen (derzeit rund 12%).
CdTe-Halbleiter:
Cadmiumtellurid hat unter anderem den Vorteil, dass es – durch simple thermische Verdampfung bei rund 500 Grad – einfach und sehr gleichmäßig auf ein Substrat abgeschieden werden kann.
Einziges Problem: Cadmiumtellurid lässt sich nur schwer negativ dotieren. Deshalb folgt auf die TCO-Schicht zunächst eine hauchdünne, rund 0,15 µm dicke Lage aus Cadmium-Sulfid: sie ist der n-dotierte Halbleiter.
Erst danach kommt die ca. 3 µm dicke p-dotierte Schicht aus CdTe, durch die der wichtige pn-Übergang entsteht; noch vor einem Jahrzehnt waren Schichtstärken von 5 bis 10 Mikrometern die Regel.
Die abschließenden Schichten von Dünnschichtmodulen im Superstrat-Aufbau sind schließlich wieder für alle Technologien identisch.
Auf das jeweilige Halbleitermaterial der Dünnschichtzelle kommt die ca. 0,7 µm dicke Rückkontakt-Lage aus Aluminium (Silber bei mikromorphen Zellen). Sie schließt – wenn die PV-Module einmal zu einer PV-Anlage verschaltet sind – den Stromkreis und lässt die aus dem Licht gewonnene elektrische Energie fließen. Verkapselt, sprich vor Umwelteinflüssen geschützt, werden die Dünnschicht-Module wie Glas-Folien-Module – durch eine EVA-Folien, auf der eine Rückscheibe auflaminiert wird.
Ein Metallrahmen zur Versteifung ist meist nicht notwendig: Denn die fertigen Module werden bei der Montage in einen vorbereiteten Alu- oder Edelstahlrahmen eingeklemmt.
Amorphes Silizium:
Die einzelnen Schichten des amorphen Siliziums werden mit Hilfe der plasmaunterstützten Gasphasenabscheidung (PECVD-Verfahren) bei rund 200 Grad aufgedampft.
Als erstes lagert sich positiv-dotiertes Silizium auf der TCO-Schicht ab, danach folgt undotiertes (intrinsisches) und schließlich negativ-dotiertes Silizium. Aufgrund der Schichtenfolge positiv – intrinsich – negativ sprechen Experten von der pin-Zelle.
Da das aufgedampfte Silizium keine geordnete Struktur aufweist, wird es als amorph (d.h. „unstrukturiert“) bezeichnet. Die vielen offenen Bindungen des Materials sind auch der Grund für den relativ schlechten Wirkungsgrad (7-8%).
Die intrinsische Schicht ist 0,2 bis 0,4 µm dick und absorbiert den Großteil des Lichts. Die positiv und negativ dotierten Lagen messen hingegen nur rund 10 Nanometer, d.h. 10 Millionstel Millimeter – für die Funktion der Solarzelle sind sie aber ebenso entscheidend: Erst durch den pn-Übergang zwischen der positiv- und negativ-dotierten Schicht können die vom Licht erzeugten Elektronen in nutzbaren Strom verwandelt werden.
Der Typische Aufbau von Dünnschichtzellen aus amorphem Silizium beträgt damit 2 bis 4 µm.
Mikromorphes Silizium: Eine relativ junge, vielversprechende Variante dieser Technologie sind Dünnschichtzellen aus mikromorphem Silizium. Hergestellt werden sie ebenfalls im PECVD-Verfahren: Auf eine rund 0,25 µm dicke amorphe Siliziumschicht dampft man hier aber mikrokristalline Siliziumpartikel auf, die deutlich kleiner als 1 Mikrometer sind.
Sie finden sich im amorphen Silizium zu kleinen Konglomeraten zusammen und bilden gemeinsam eine 1 bis 4 Mikrometer starke mikromorphe Solarzelle. Der Vorteil: Weil sich mikrokristallines wie kristallines Silizium verhält, können diese Zellen das Sonnenspektrum besser nutzen und so einen signifikant höheren Wirkungsgrad erzielen (derzeit rund 12%).
CdTe-Halbleiter:
Cadmiumtellurid hat unter anderem den Vorteil, dass es – durch simple thermische Verdampfung bei rund 500 Grad – einfach und sehr gleichmäßig auf ein Substrat abgeschieden werden kann.
Einziges Problem: Cadmiumtellurid lässt sich nur schwer negativ dotieren. Deshalb folgt auf die TCO-Schicht zunächst eine hauchdünne, rund 0,15 µm dicke Lage aus Cadmium-Sulfid: sie ist der n-dotierte Halbleiter.
Erst danach kommt die ca. 3 µm dicke p-dotierte Schicht aus CdTe, durch die der wichtige pn-Übergang entsteht; noch vor einem Jahrzehnt waren Schichtstärken von 5 bis 10 Mikrometern die Regel.
Die abschließenden Schichten von Dünnschichtmodulen im Superstrat-Aufbau sind schließlich wieder für alle Technologien identisch.
Auf das jeweilige Halbleitermaterial der Dünnschichtzelle kommt die ca. 0,7 µm dicke Rückkontakt-Lage aus Aluminium (Silber bei mikromorphen Zellen). Sie schließt – wenn die PV-Module einmal zu einer PV-Anlage verschaltet sind – den Stromkreis und lässt die aus dem Licht gewonnene elektrische Energie fließen. Verkapselt, sprich vor Umwelteinflüssen geschützt, werden die Dünnschicht-Module wie Glas-Folien-Module – durch eine EVA-Folien, auf der eine Rückscheibe auflaminiert wird.
Ein Metallrahmen zur Versteifung ist meist nicht notwendig: Denn die fertigen Module werden bei der Montage in einen vorbereiteten Alu- oder Edelstahlrahmen eingeklemmt.
Die CIG-Zelle und der Substrat-Aufbau
Beim Substrat-Aufbau stellen die Modulhersteller die gerade beschriebene Schichtfolge auf den Kopf.
Zwar dient auch hier eine Glasscheibe als Trägermaterial, sie liegt aber auf der lichtabgewandten Unterseite des Dünnschichtmoduls (daher sub-, lat. für unter).
Die umgekehrte Schichtfolge und das Halbleitermaterial Kupfer-Indium-Selenid ziehen außerdem einige kleine Anpassungen im Aufbau des Dünnschichtmoduls nach sich.
Auf die tragende Glasscheibe bringt man zuerst eine Schicht aus Siliziumnitrid auf (Si3N4).
Sie verhindert, dass Fremdatome aus dem Trägerglas in das darüber liegende Solarzellenmaterial gelangen.
Diese Verunreinigungen würden den Wirkungsgrad der Zelle verschlechtern.
Auf diese Sperrschicht folgt der Rückseitenkontakt, der bei CIS-Modulen aus Molybdän, einem bleiartig glänzenden Metall, besteht. (Manche Hersteller vertauschen die Reihenfolge von Sperrschicht und Kontakt; das kann hier jedoch vernachlässigt werden.)
Das eigentliche Solarzellenmaterial, den Kupferkies CIS, dampfen die Hersteller wie Cadmiumtellurid bei rund 500 Grad einfach auf das Molybdän auf.
Es genügt in diesem Fall eine Schichtstärke von 1,5 µm, um den Großteil des Sonnenlichts einzufangen und in elektrischen Strom umzuwandeln.
Steuern können die Hersteller den Anteil des absorbierten Lichtspektrums über die Indium-Konzentration.
Der Wirkungsgrad lässt sich durch die Beimengungen von Gallium erhöhen, wodurch CIGS-Module aus Kupfer-Indium-Gallium-Selenid entstehen.
CIS-Photovoltaik-Modul: der Fenstertrick
CIS Fenster
Den Abschluss des zentralen Aufbau des CIG/CIGS-Moduls bildet das so genannte Fenster: PV-Ingenieure nennen so die drei hauchdünnen Lagen über der Absorberschicht aus Chalkopyrit.
Direkt über dem p-dotierten Verbindungshalbleiter Kupfer-Indium-(Gallium)-Selenid folgt eine 40 bis 50 Nanometer starke n-dotierte Pufferschicht aus Cadmium-Selenid (CdS). Ihre Aufgabe ist es, die hochsensible CIS-Solarzellenschicht zu schützen und Einbußen beim Wirkungsgrad zu verhindern.
Abgeschieden wird das Cadmium-Selenid in einem chemischen Wasserbad – und genau das ist den Herstellern ein Dorn im Auge. Als einziges nass-chemisches Verfahren verkompliziert und verteuert dieser Prozess die Herstellung; außerdem enthält der Puffer - in winzigen Spuren - das schädliche Cadmium, das ganz aus der CIGS-Zelle verbannt werden soll.
Bisher waren alle Versuche, die Pufferschicht zu ersetzen, vergeblich.
Forscher des Helmholz Zentrums Berlin haben nun aber eine Möglichkeit gefunden, die CdS-Schicht vollwertig zu ersetzen. Sie modifizieren die darüber liegende transparente Zinkoxidschicht (TCO) durch Zugabe von Sauerstoff und Schwefel so, dass sie die Funktion der Pufferschicht übernehmen kann.
Der nass-chemische Prozessschritt und das Cadmium-Selenid werden damit überflüssig.
Die 0,4 bis 0,6 µm dünne TCO-Schicht steigt im CIGS-Modul damit zu einer der wichtigsten Lagen auf: Neben der Funktion als elektrischer Leiter und Puffer fungiert sie - ob ihrer hohen Lichtdurchlässigkeit - als „Lichtfänger“: als erste Schicht des „Fensters“.
Die zweite Lage des Fensters ist ebenfalls aus Zinkoxid, das mit Aluminium n-dotiert wird. Diese Schicht stellt sicher, dass der pn-Übergang tief in die CIGS-Absorberschicht reicht und das Modul effizient arbeitet.
Das CIS/CIGS-Rohmodul ist nach Aufbringung der drei „Fenster“-Schichten fertig.
Jetzt muss es noch für den Einsatz in der Praxis gewappnet werden - was wiederum durch den Schritt der Verkapselung erfolgt.
Das Rohmodul wird zu diesem Zweck von den elektrisch aktiven Schichten an den Rändern befreit („Rand-Entschichtung“) und rundum mit einem Dichtungsband aus Kunststoff oder Kautschuk versehen.
Über der TCO-Schicht wird die Laminatfolie aus Ethylen-Vinyl-Acetat aufgelegt, erhitzt und mit dem antireflexbeschichteten Abdeckglas verklebt.
Hiermit ist auch die Versiegelung des CIGS-Moduls abgeschlossen. Nach der Einfassung mit einem Edelstahl- oder Aluminiumrahmen kann es montiert werden.
Aufbau Photovoltaikmodule: Meisterwerk solarer Ingenieurskunst
FAZIT
Von außen macht ein PV-Modul nicht den kompliziertesten Eindruck. Ein detaillierter Blick auf den Aufbau von Photovoltaikmodulen zeigt aber: Solarmodule sind Meisterwerke moderner Ingenieurskunst – und zwar Schicht für Schicht. Paneele aus kristallinen Solarzellen ebenso wie Dünnschichtmodule (s.a. Vergleich von Dick- und Dünnschichtmodulen).
Der technische und materielle Aufwand lohnt sich:
Mit PV-Modulen, die so sorgfältig aufgebaut und hergestellt werden wie gezeigt, können Sie über 20 bis 40 Jahre lang reichlich Solarstrom ernten - in Deutschland pro Kilowatt Modulleisten z.B. zwischen 800 und 1.250 kWh pro Jahr, je nach Standort.
Die bei der Produktion aufgewendete Energie ist in 1 bis 3 Jahren wieder eingebracht.
Die Kosten für die Stromerzeugung sind mit 10 bis 15 Cent/kWh nur halb so teuer wie die für zugekauften Haushaltsstrom.

Die CIG-Zelle und der Substrat-Aufbau
Beim Substrat-Aufbau stellen die Modulhersteller die gerade beschriebene Schichtfolge auf den Kopf.
Zwar dient auch hier eine Glasscheibe als Trägermaterial, sie liegt aber auf der lichtabgewandten Unterseite des Dünnschichtmoduls (daher sub-, lat. für unter).
Die umgekehrte Schichtfolge und das Halbleitermaterial Kupfer-Indium-Selenid ziehen außerdem einige kleine Anpassungen im Aufbau des Dünnschichtmoduls nach sich.
Auf die tragende Glasscheibe bringt man zuerst eine Schicht aus Siliziumnitrid auf (Si3N4).
Sie verhindert, dass Fremdatome aus dem Trägerglas in das darüber liegende Solarzellenmaterial gelangen.
Diese Verunreinigungen würden den Wirkungsgrad der Zelle verschlechtern.
Auf diese Sperrschicht folgt der Rückseitenkontakt, der bei CIS-Modulen aus Molybdän, einem bleiartig glänzenden Metall, besteht. (Manche Hersteller vertauschen die Reihenfolge von Sperrschicht und Kontakt; das kann hier jedoch vernachlässigt werden.)
Das eigentliche Solarzellenmaterial, den Kupferkies CIS, dampfen die Hersteller wie Cadmiumtellurid bei rund 500 Grad einfach auf das Molybdän auf.
Es genügt in diesem Fall eine Schichtstärke von 1,5 µm, um den Großteil des Sonnenlichts einzufangen und in elektrischen Strom umzuwandeln.
Steuern können die Hersteller den Anteil des absorbierten Lichtspektrums über die Indium-Konzentration.
Der Wirkungsgrad lässt sich durch die Beimengungen von Gallium erhöhen, wodurch CIGS-Module aus Kupfer-Indium-Gallium-Selenid entstehen.
CIS-Photovoltaik-Modul: der Fenstertrick
CIS Fenster
Den Abschluss des zentralen Aufbau des CIG/CIGS-Moduls bildet das so genannte Fenster: PV-Ingenieure nennen so die drei hauchdünnen Lagen über der Absorberschicht aus Chalkopyrit.
Direkt über dem p-dotierten Verbindungshalbleiter Kupfer-Indium-(Gallium)-Selenid folgt eine 40 bis 50 Nanometer starke n-dotierte Pufferschicht aus Cadmium-Selenid (CdS). Ihre Aufgabe ist es, die hochsensible CIS-Solarzellenschicht zu schützen und Einbußen beim Wirkungsgrad zu verhindern.
Abgeschieden wird das Cadmium-Selenid in einem chemischen Wasserbad – und genau das ist den Herstellern ein Dorn im Auge. Als einziges nass-chemisches Verfahren verkompliziert und verteuert dieser Prozess die Herstellung; außerdem enthält der Puffer - in winzigen Spuren - das schädliche Cadmium, das ganz aus der CIGS-Zelle verbannt werden soll.
Bisher waren alle Versuche, die Pufferschicht zu ersetzen, vergeblich.
Forscher des Helmholz Zentrums Berlin haben nun aber eine Möglichkeit gefunden, die CdS-Schicht vollwertig zu ersetzen. Sie modifizieren die darüber liegende transparente Zinkoxidschicht (TCO) durch Zugabe von Sauerstoff und Schwefel so, dass sie die Funktion der Pufferschicht übernehmen kann.
Der nass-chemische Prozessschritt und das Cadmium-Selenid werden damit überflüssig.
Die 0,4 bis 0,6 µm dünne TCO-Schicht steigt im CIGS-Modul damit zu einer der wichtigsten Lagen auf: Neben der Funktion als elektrischer Leiter und Puffer fungiert sie - ob ihrer hohen Lichtdurchlässigkeit - als „Lichtfänger“: als erste Schicht des „Fensters“.
Die zweite Lage des Fensters ist ebenfalls aus Zinkoxid, das mit Aluminium n-dotiert wird. Diese Schicht stellt sicher, dass der pn-Übergang tief in die CIGS-Absorberschicht reicht und das Modul effizient arbeitet.
Das CIS/CIGS-Rohmodul ist nach Aufbringung der drei „Fenster“-Schichten fertig.
Jetzt muss es noch für den Einsatz in der Praxis gewappnet werden - was wiederum durch den Schritt der Verkapselung erfolgt.
Das Rohmodul wird zu diesem Zweck von den elektrisch aktiven Schichten an den Rändern befreit („Rand-Entschichtung“) und rundum mit einem Dichtungsband aus Kunststoff oder Kautschuk versehen.
Über der TCO-Schicht wird die Laminatfolie aus Ethylen-Vinyl-Acetat aufgelegt, erhitzt und mit dem antireflexbeschichteten Abdeckglas verklebt.
Hiermit ist auch die Versiegelung des CIGS-Moduls abgeschlossen. Nach der Einfassung mit einem Edelstahl- oder Aluminiumrahmen kann es montiert werden.
Aufbau Photovoltaikmodule: Meisterwerk solarer Ingenieurskunst
FAZIT
Von außen macht ein PV-Modul nicht den kompliziertesten Eindruck. Ein detaillierter Blick auf den Aufbau von Photovoltaikmodulen zeigt aber: Solarmodule sind Meisterwerke moderner Ingenieurskunst – und zwar Schicht für Schicht. Paneele aus kristallinen Solarzellen ebenso wie Dünnschichtmodule (s.a. Vergleich von Dick- und Dünnschichtmodulen).
Der technische und materielle Aufwand lohnt sich:
Mit PV-Modulen, die so sorgfältig aufgebaut und hergestellt werden wie gezeigt, können Sie über 20 bis 40 Jahre lang reichlich Solarstrom ernten - in Deutschland pro Kilowatt Modulleisten z.B. zwischen 800 und 1.250 kWh pro Jahr, je nach Standort.
Die bei der Produktion aufgewendete Energie ist in 1 bis 3 Jahren wieder eingebracht.
Die Kosten für die Stromerzeugung sind mit 10 bis 15 Cent/kWh nur halb so teuer wie die für zugekauften Haushaltsstrom.

Die CIG-Zelle und der Substrat-Aufbau
Beim Substrat-Aufbau stellen die Modulhersteller die gerade beschriebene Schichtfolge auf den Kopf.
Zwar dient auch hier eine Glasscheibe als Trägermaterial, sie liegt aber auf der lichtabgewandten Unterseite des Dünnschichtmoduls (daher sub-, lat. für unter).
Die umgekehrte Schichtfolge und das Halbleitermaterial Kupfer-Indium-Selenid ziehen außerdem einige kleine Anpassungen im Aufbau des Dünnschichtmoduls nach sich.
Auf die tragende Glasscheibe bringt man zuerst eine Schicht aus Siliziumnitrid auf (Si3N4).
Sie verhindert, dass Fremdatome aus dem Trägerglas in das darüber liegende Solarzellenmaterial gelangen.
Diese Verunreinigungen würden den Wirkungsgrad der Zelle verschlechtern.
Auf diese Sperrschicht folgt der Rückseitenkontakt, der bei CIS-Modulen aus Molybdän, einem bleiartig glänzenden Metall, besteht. (Manche Hersteller vertauschen die Reihenfolge von Sperrschicht und Kontakt; das kann hier jedoch vernachlässigt werden.)
Das eigentliche Solarzellenmaterial, den Kupferkies CIS, dampfen die Hersteller wie Cadmiumtellurid bei rund 500 Grad einfach auf das Molybdän auf.
Es genügt in diesem Fall eine Schichtstärke von 1,5 µm, um den Großteil des Sonnenlichts einzufangen und in elektrischen Strom umzuwandeln.
Steuern können die Hersteller den Anteil des absorbierten Lichtspektrums über die Indium-Konzentration.
Der Wirkungsgrad lässt sich durch die Beimengungen von Gallium erhöhen, wodurch CIGS-Module aus Kupfer-Indium-Gallium-Selenid entstehen.
CIS-Photovoltaik-Modul: der Fenstertrick
CIS Fenster
Den Abschluss des zentralen Aufbau des CIG/CIGS-Moduls bildet das so genannte Fenster: PV-Ingenieure nennen so die drei hauchdünnen Lagen über der Absorberschicht aus Chalkopyrit.
Direkt über dem p-dotierten Verbindungshalbleiter Kupfer-Indium-(Gallium)-Selenid folgt eine 40 bis 50 Nanometer starke n-dotierte Pufferschicht aus Cadmium-Selenid (CdS). Ihre Aufgabe ist es, die hochsensible CIS-Solarzellenschicht zu schützen und Einbußen beim Wirkungsgrad zu verhindern.
Abgeschieden wird das Cadmium-Selenid in einem chemischen Wasserbad – und genau das ist den Herstellern ein Dorn im Auge. Als einziges nass-chemisches Verfahren verkompliziert und verteuert dieser Prozess die Herstellung; außerdem enthält der Puffer - in winzigen Spuren - das schädliche Cadmium, das ganz aus der CIGS-Zelle verbannt werden soll.
Bisher waren alle Versuche, die Pufferschicht zu ersetzen, vergeblich.
Forscher des Helmholz Zentrums Berlin haben nun aber eine Möglichkeit gefunden, die CdS-Schicht vollwertig zu ersetzen. Sie modifizieren die darüber liegende transparente Zinkoxidschicht (TCO) durch Zugabe von Sauerstoff und Schwefel so, dass sie die Funktion der Pufferschicht übernehmen kann.
Der nass-chemische Prozessschritt und das Cadmium-Selenid werden damit überflüssig.
Die 0,4 bis 0,6 µm dünne TCO-Schicht steigt im CIGS-Modul damit zu einer der wichtigsten Lagen auf: Neben der Funktion als elektrischer Leiter und Puffer fungiert sie - ob ihrer hohen Lichtdurchlässigkeit - als „Lichtfänger“: als erste Schicht des „Fensters“.
Die zweite Lage des Fensters ist ebenfalls aus Zinkoxid, das mit Aluminium n-dotiert wird. Diese Schicht stellt sicher, dass der pn-Übergang tief in die CIGS-Absorberschicht reicht und das Modul effizient arbeitet.
Das CIS/CIGS-Rohmodul ist nach Aufbringung der drei „Fenster“-Schichten fertig.
Jetzt muss es noch für den Einsatz in der Praxis gewappnet werden - was wiederum durch den Schritt der Verkapselung erfolgt.
Das Rohmodul wird zu diesem Zweck von den elektrisch aktiven Schichten an den Rändern befreit („Rand-Entschichtung“) und rundum mit einem Dichtungsband aus Kunststoff oder Kautschuk versehen.
Über der TCO-Schicht wird die Laminatfolie aus Ethylen-Vinyl-Acetat aufgelegt, erhitzt und mit dem antireflexbeschichteten Abdeckglas verklebt.
Hiermit ist auch die Versiegelung des CIGS-Moduls abgeschlossen. Nach der Einfassung mit einem Edelstahl- oder Aluminiumrahmen kann es montiert werden.
Aufbau Photovoltaikmodule: Meisterwerk solarer Ingenieurskunst
FAZIT
Von außen macht ein PV-Modul nicht den kompliziertesten Eindruck. Ein detaillierter Blick auf den Aufbau von Photovoltaikmodulen zeigt aber: Solarmodule sind Meisterwerke moderner Ingenieurskunst – und zwar Schicht für Schicht. Paneele aus kristallinen Solarzellen ebenso wie Dünnschichtmodule (s.a. Vergleich von Dick- und Dünnschichtmodulen).
Der technische und materielle Aufwand lohnt sich:
Mit PV-Modulen, die so sorgfältig aufgebaut und hergestellt werden wie gezeigt, können Sie über 20 bis 40 Jahre lang reichlich Solarstrom ernten - in Deutschland pro Kilowatt Modulleisten z.B. zwischen 800 und 1.250 kWh pro Jahr, je nach Standort.
Die bei der Produktion aufgewendete Energie ist in 1 bis 3 Jahren wieder eingebracht.
Die Kosten für die Stromerzeugung sind mit 10 bis 15 Cent/kWh nur halb so teuer wie die für zugekauften Haushaltsstrom.
